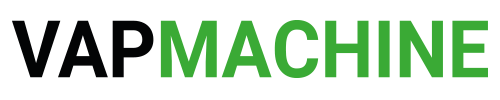
ELECTRICITY AND HEAT FROM BIOMASS
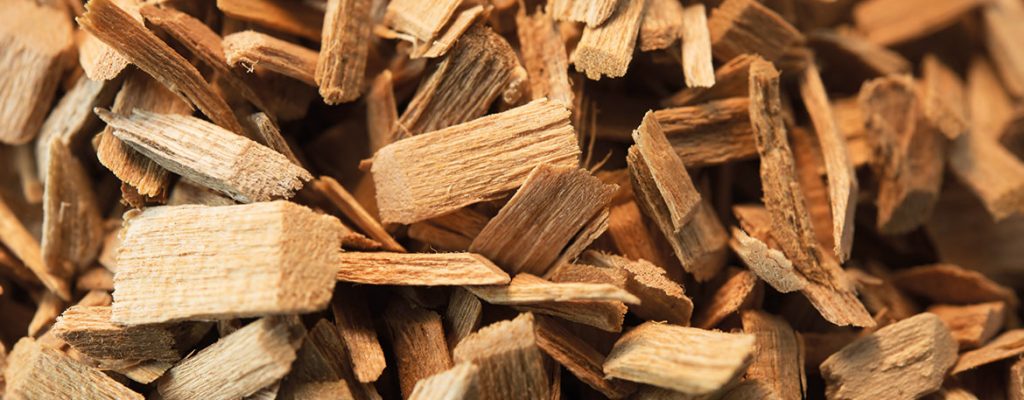
THE COMBINED HEAT AND POWER SYSTEM
(CHP SYSTEM) WITH BIOMASS COMBUSTION
AND STEAM MOTOR
Electrical power: up to 100 kW
Thermal recovery: approx. 400 kW
per system, multiple versions possible
SYSTEM FUNCTIONALITY
Biomass is combusted efficiently at a high temperature in a specially developed furnace. The heat that is generated is emitted to a closed circuit with distilled water using an exchanger. This process creates steam. The steam drives a piston motor with an integrated generator. After the motor, the residual steam is condensed, fed back into the furnace and the heat is emitted to a separate water circuit, which is used as hot water.
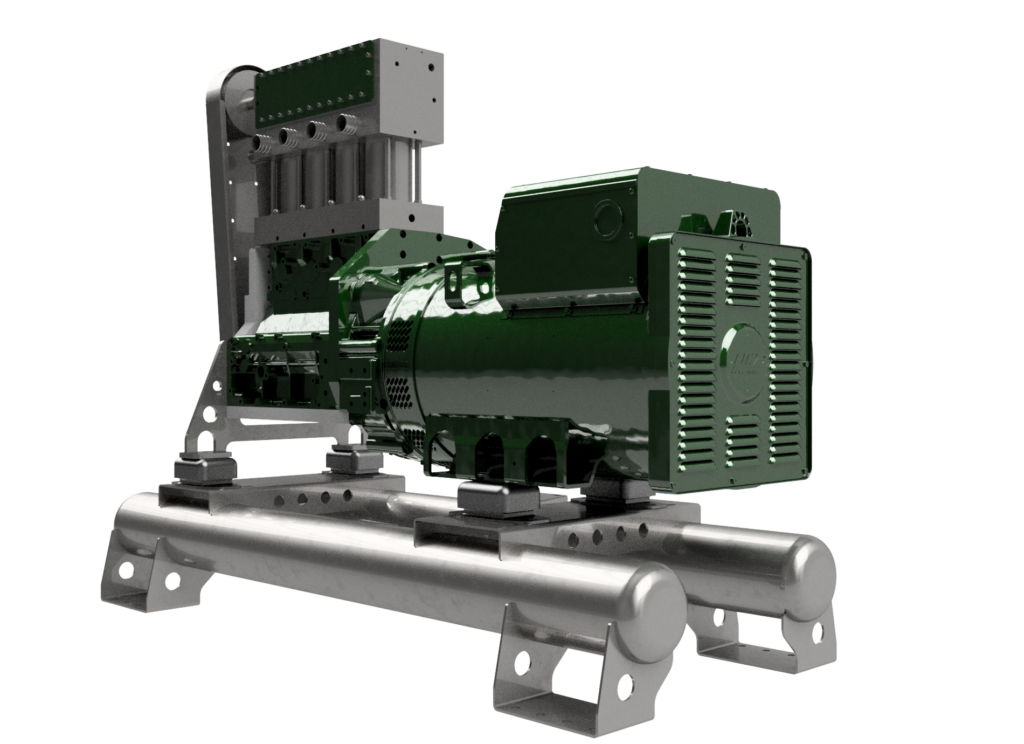
Biomass cogeneration plant VAP 500
The steam power plant for heat and power generation
Our standardised biomass cogeneration plants are delivered ready for connection. They are pre-installed, piped and wired in specially designed containers. The modular container design enables the simple and uncomplicated parallel connection of several plants. Subsequent expansion with additional plants is also uncomplicated and cost-effective.
A fully automatic biomass conveyor system for feeding the kiln can be adapted according to customer requirements. And can provide weeks of autonomy for the plant.
Power: 100kW electric and 400kW thermal
Container dimensions (LxWxH): 10m x 2.5m x 3m
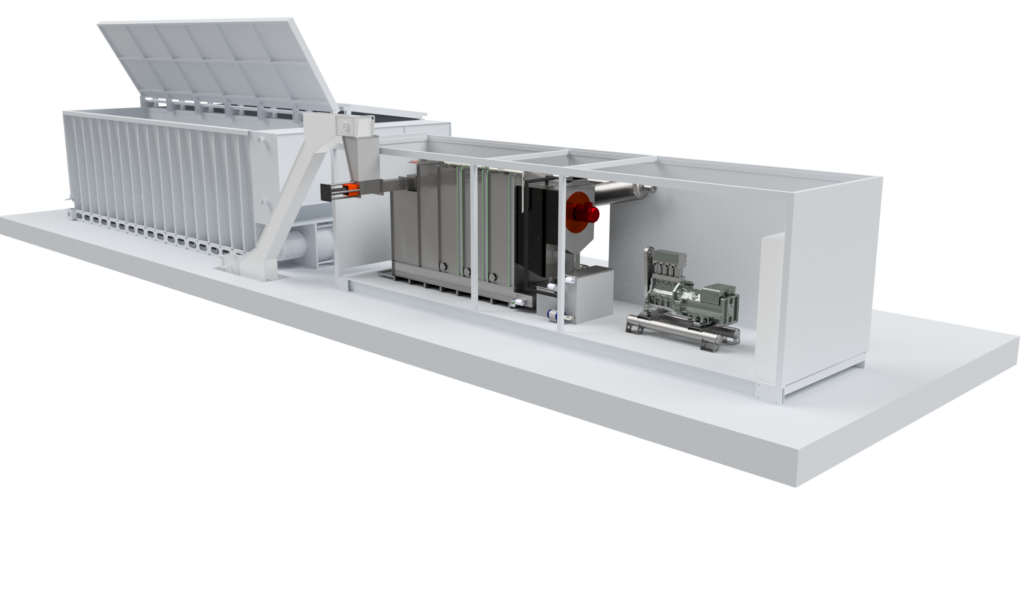
THE KEY ADVANTAGES OF A BIOMASS COGENERATION PLANT
The combustion process is fully automatic, the presence of personnel is rarely necessary, especially since the combustion materials are fed in via a specially designed feeder. This is insensitive, quiet and requires little energy. The conveyor system can be adapted to customer requirements and can provide weeks of autonomy for the plant.
The combustion chamber of the newly-developed furnace is designed for temperatures of between 1,200 °C and 1,400 °C, which is why the level of tolerance in terms of the combustion materials that are used is very high. Even material of a lower quality can be used. For this reason, there is a large amount of variety in terms of the materials that can be used and these range from biomass and fossil fuels to materials from the disposal sector.
The steam exchanger, which was also specially developed for this system, stabilises the steam production by means of heat storage in metal mass; steam production only takes place in a continuous flow and without additional storage.
The newly developed steam engine is a 4-cylinder piston expansion engine with a generating torque of up to 650Nm. The steam engine runs at a speed of 1500 rpm and is connected directly to the mains via a generator coupling. A unique sealing concept allows oil lubrication of the components while keeping the steam circuit clean. This increases the service life of the unit components and reduces the maintenance requirements of the plant.
The modular container design enables high flexibility and scalability of the system design. Our plants can be easily connected in parallel and subsequent expansions are also simple. During maintenance work, a single plant can be shut down while other plants continue to operate. The installation of a plant is quick and easy.
THE CORE COMPONENTS OF THE SYSTEM
Biomass furnace
The furnace combustion chamber is designed such that the combustion temperature can be held at between 1,200 °C and 1,400 °C. This is made possible by the special hanging riddle grate and accelerated primary air and secondary air. The grate almost entirely prevents slagging too. In order to be able to respond to the calorific value content of various types of biomass, the hanging grate is adjustable and the combustion chamber can be made larger or smaller according to the requirements. In the event of more minor differences in the biomass (drier or damper material), the system responds automatically via the accelerated combustion air and subsequently also in the feeding. The high combustion temperatures keep the exhaust values very low. The ash formation ranges, depending on the combustion material, from between 0.5 and 5%, whereby this can be used as a high-quality fertiliser.
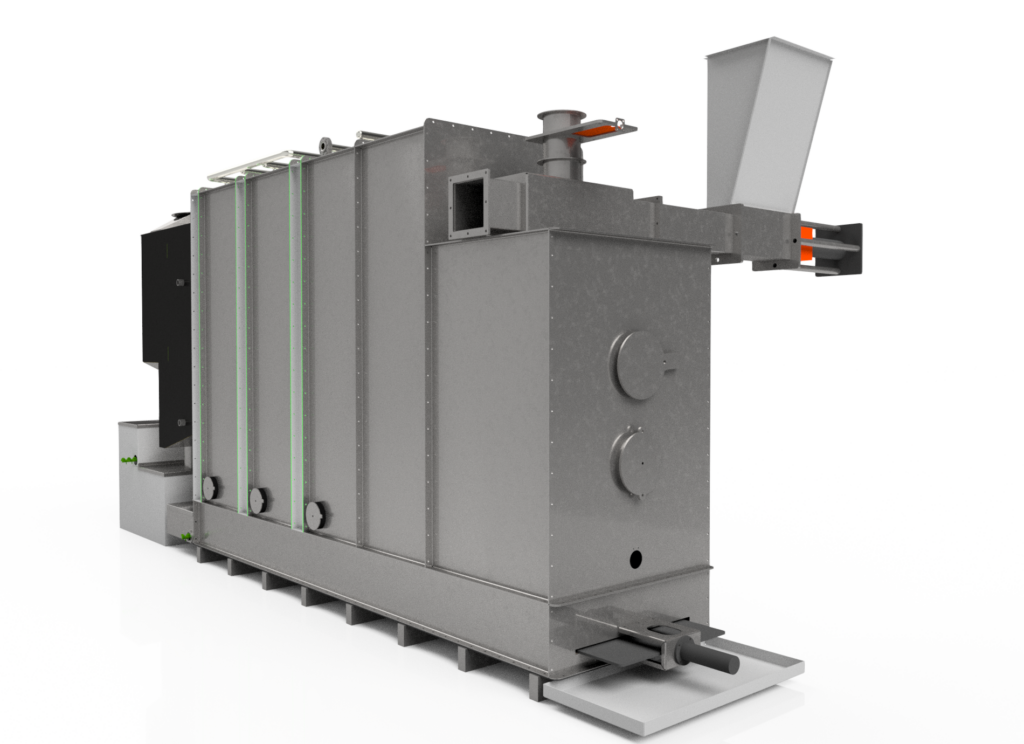

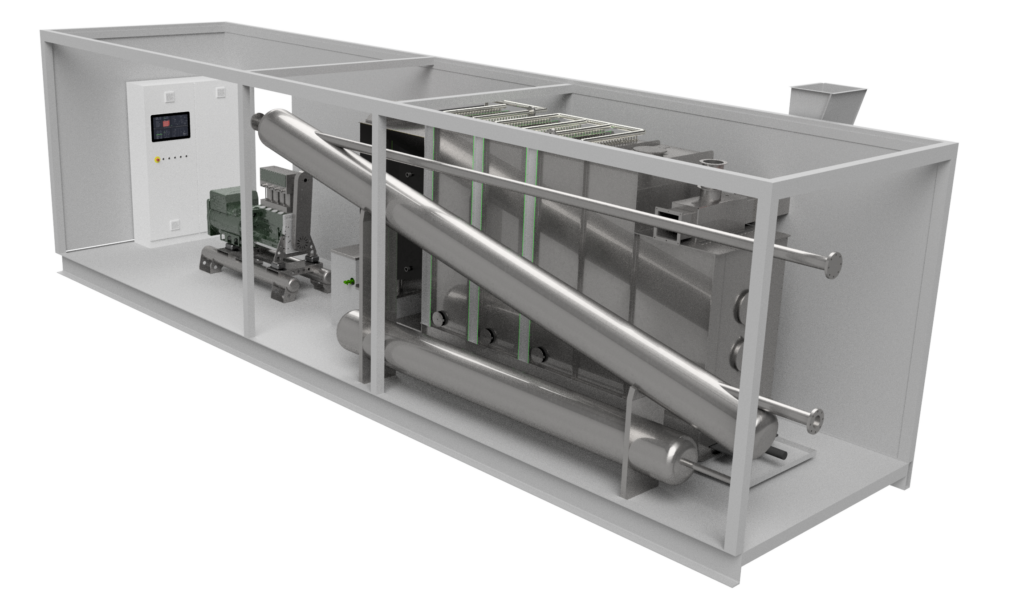
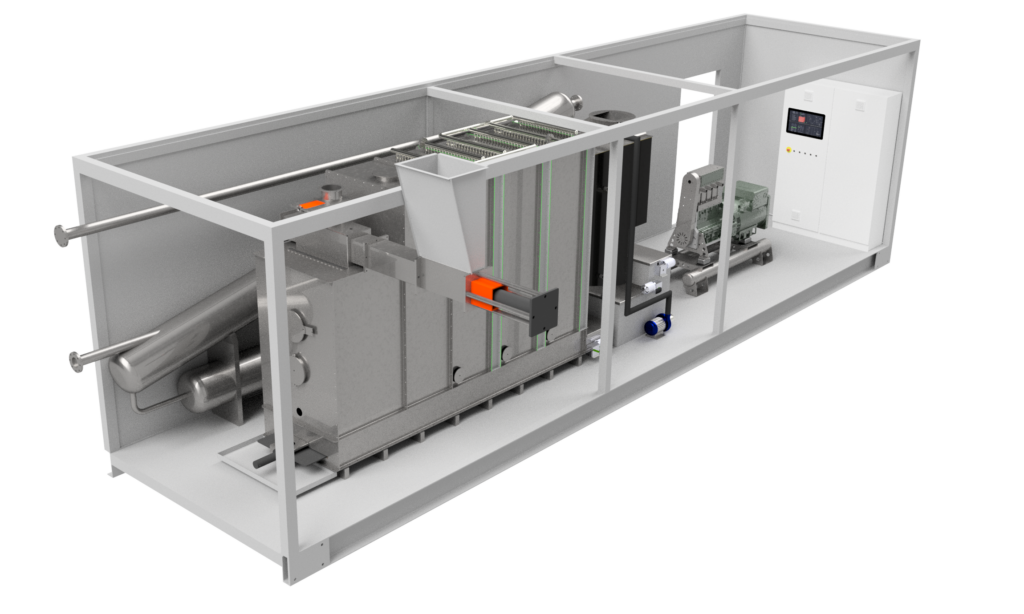
Steam exchanger,
Flow steam production
The steam exchanger is one of the core components of the system. It has a sufficient exchanger area and a correspondingly large quantity of metal, which stores the heat. This facilitates continuous steam production (max. steam temperature 500 °C) in the flow whilst using a relatively low quantity of water. This avoids the costs of intensive monitoring by a boiler operator. The steam controlled system facilitates precise control of the steam pressure from 0 bar to a maximum of 50 bar.
Electricity production with steam engine
The engine, like the furnace and steam exchanger, is also a new development and the product of decades of experience in similar applications.
The 4-cylinder piston expansion engine runs at a speed of 1500rpm and can generate up to 650Nm of torque. The engine’s specially designed valve head has preset steam injection and exhaust times designed for best possible performance and efficiency at the rated speed of 1500rpm and process pressures up to 45bar. The process control section can regulate the motor performance for maximum yield even with fluctuations in fuel quality. The unique sealing concept of the machine enables the allmost perfect separation of the steam circuit medium and the lubricant. This allows oil lubrication of the machine components while avoiding mutual contamination of the media. Consequently, complex separation devices are not necessary. Via the directly coupled generator, the unit can be connected in parallel to the mains and feed power of up to 100 kW into the mains.
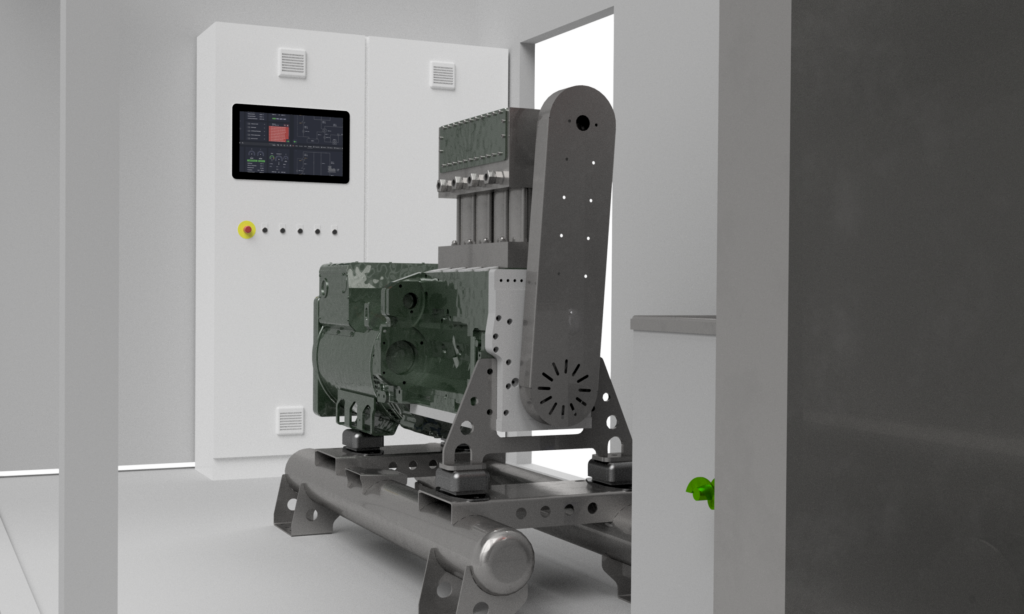
HYDRAULIC STEAM VALVES
The DDRV and DSV hydraulic shut-off and control valves are specially designed for the dynamics of steam and impress with their high robustness and durability at comparatively low cost. While the hydraulic shut-off valve DSV is responsible for the fast switching on and off of a pipe, the control valve DDRV is used for the phase-free regulation of the opening degree.
Control valve DDRV 1000/50
Pressure: 0-50bar
Mass flow: 0-1000kg/h
Fluid temperature: 100-500°C
Material: Stainless steel
Control: 4…20mA
Power supply: 24V
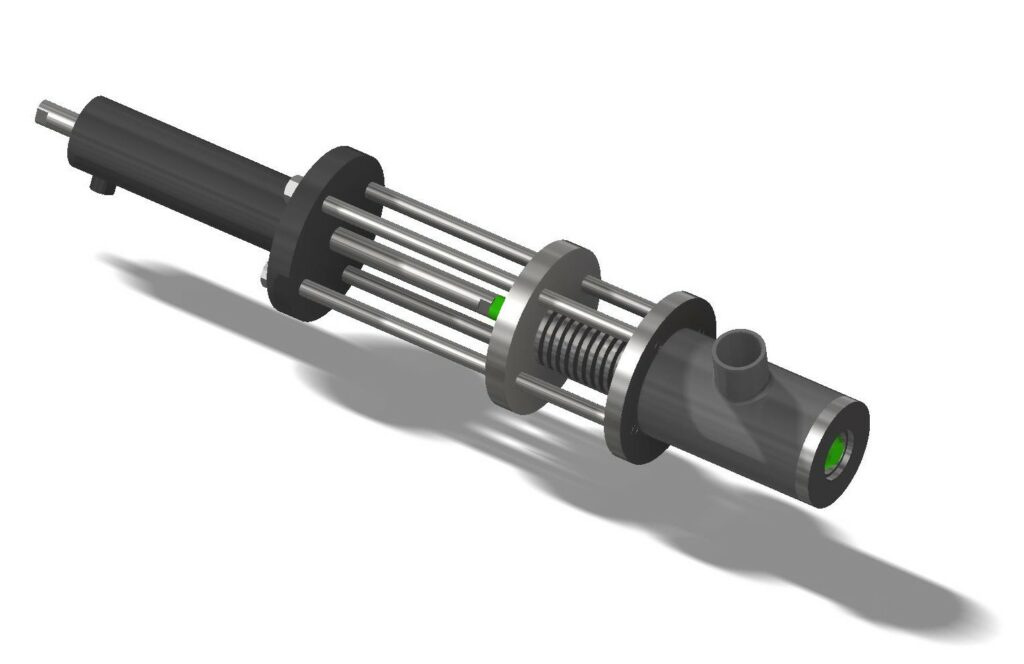
Shut-off valve 1000/50
Pressure: 0-50bar
Mass flow: 0-1000kg/h
Fluid temperature: 100-500°C
Material: Stainless steel
Control: 24V (NO/NC)
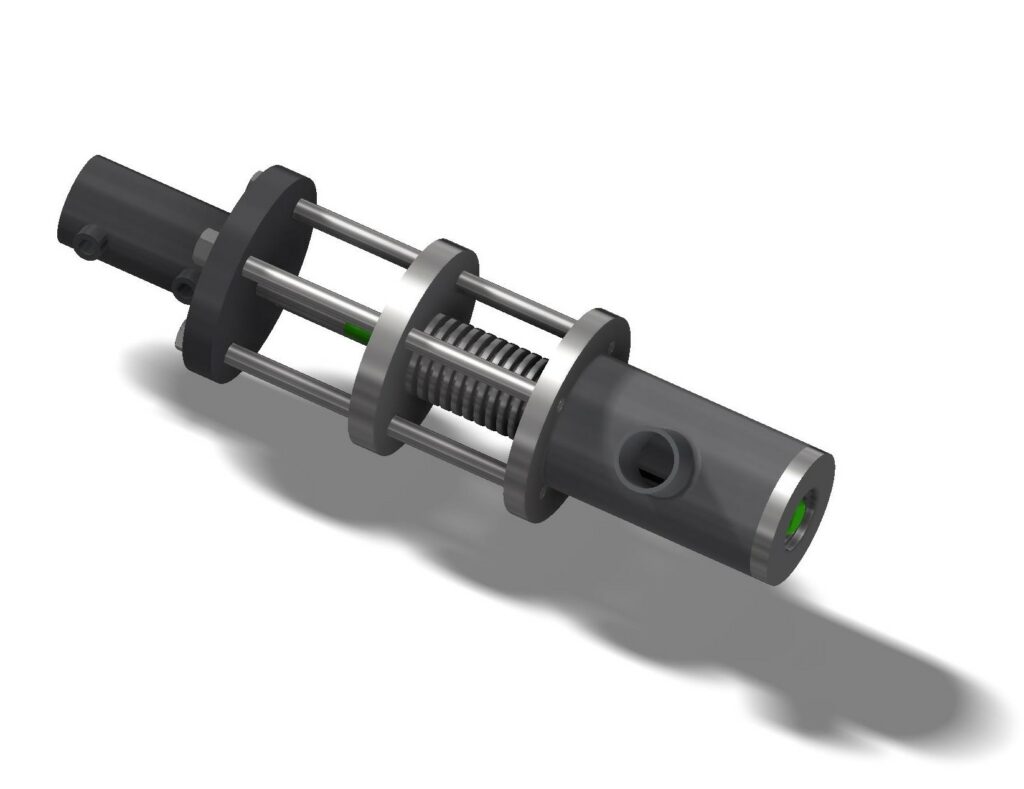
WORKING TIME
- Mon–Fri: 08:00–18:00